Choosing the Right Drive System for Your Robotics Application: Electric, Hydraulic, and Pneumatic Drives Explained
Robots do dirty, difficult, and dangerous jobs. From welding and painting car bodies to applying adhesives, packing candies and loading pallets, they help manufacturers reduce waste and become more productive.
Every industrial robot has a drive system that generates the movements needed. Understanding the differences between these systems is key to successful selection and integration. This article introduces the three drive technologies used, highlights their strengths, and describes where each is used.
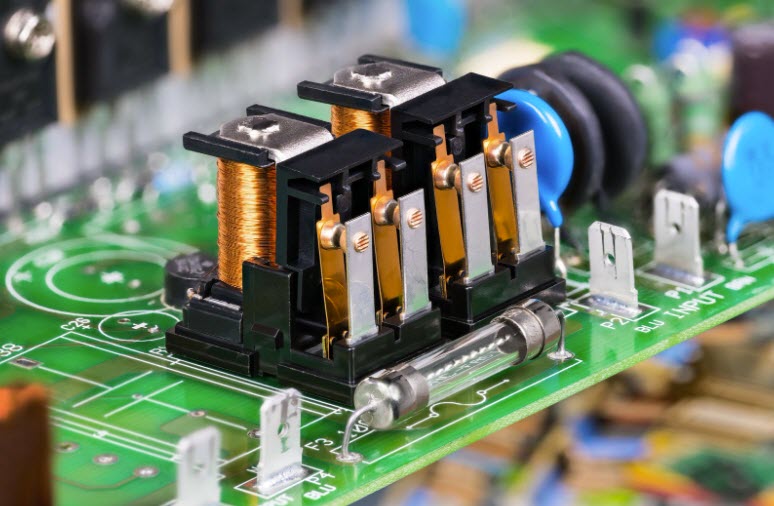
Industrial Robot Basics
The drive system provides the motion a robot needs to perform the task assigned. The main types of robots used in industry today are:
- Articulated: Six axis arms where each joint moves through an arc.
- Cartesian: Moves in straight lines, typically has three axes.
- Delta: Parallel link arms typically suspended above a conveyor, move very fast over short distances.
SCARA: Short for Selective Compliance Articulated Robot Arm, provides four axes of rapid rotational movement.
Readers may also encounter collaborative robots or “cobots”. These are designed to work in close proximity with human workers. Most commercially available cobots are of the articulated arm configuration.
Robots are programmed by providing the coordinates of a series of points that the gripper or “end effector” is to move through. This can be done using a “teach pendant” to move the end effector to each point, or with offline programming software.
The robot controller calculates where each joint should move to get the end effector to the target position. These movements are then sent as commands to the drive system components.
The majority of industrial robots use electric motors, although hydraulic and pneumatic power are preferred for some applications.
Electric Drive Systems - Advantages and Applications
Most articulated industrial robots use AC servo motors at each joint. These respond quickly and precisely to the speed and rotation commands sent by the controller. Some older and smaller robot models use DC servo or stepper motors. These are less powerful, less precise, and often slower.
SCARA and delta robots also use servo motors for rotary motion. In the case of electric-driven cartesian robots, the motor turns a leadscrew that provides linear motion.
The advantages of electric drive are:
- Very accurate and repeatable positioning
- Low maintenance
- Energy-efficient
Compact for the torque produced
Applications for electric drive robots include assembly, machine tending, packaging, painting and welding.
Hydraulic Drive Systems - Advantages and Applications
These systems use hydraulic motors, hydraulic cylinders (linear actuators with internal pistons), or a combination of the two. They also need a pump that pushes hydraulic fluid through the system.
The main reason for choosing hydraulic over electric drive is the higher power density. (That’s the power or torque produced relative to the size of the actuators.) This makes it suitable for moving very heavy loads or moving loads over extended distances where long reach is required. Applications include moving loaded pallets, very large castings or heavy machinery.
A second advantage is their smooth movement. This benefits applications involving transporting fluids or especially delicate payloads.
Pneumatic Drive Systems - Advantages and Applications
These drive systemsuse compressed air to operate linear cylinders, which makes them suitable for cartesian-style robots. Pneumatic rotary actuators are also available to provide rotary motion.
The advantages of pneumatic drive are:
- Compressed air is available in most factories (although it is an expensive energy source)
- Pneumatic actuators are inexpensive compared to electric and hydraulic components
- Pneumatic actuators can provide high-speed motion
- Assembly is less complex
Compressed air can provide cushioning at the end of a movement, something electric and hydraulic drives are less capable of
Pneumatic robots are generally used for light-duty “pick and place” operations, (where an object is grasped, lifted, moved and lowered into its new position.) They also find applications in polishing and deburring operations where their in-built compliance accommodates size variations between parts or workpieces. Many industrial robots use pneumatic grippers for the same reason.
Drive Systems: Going through the Motions
Each drive technology has its strengths: there’s no single “best” solution. Instead, the key to successful implementation is to consider what the application needs.
Choose an electric drive system for:
- Repeatable, precise movement
Low energy and maintenance costs
However, this technology is complex and more expensive than the alternatives. Neither will it provide very high forces without using big, bulky motors.
A hydraulic system is appropriate for robots intended for:
- Moving very large or heavy loads
- Long reach applications
Applications that need very smooth motion
Hydraulic systems do need regular fluid and filter changes, and seals can wear and fail. They are also less energy-efficient than electric drive systems.
Pneumatic drive systems are the least complex to install and use. (A technician comfortable with pneumatic controls and logic circuits can assemble a system by themselves.) However, their force and accuracy is limited, so this technology is reserved for situations where:
- Positioning is not critical
- Speed is desired
Simplicity and ease of assembly and integration are important considerations
When designing or developing a robotic system, consider combining technologies. This can lead to a “best of all worlds” solution. For example, a pneumatic cartesian robot could have an electric rotary actuator on the end of the raising/lowering cylinder. Alternatively, add pneumatic grippers to an electric articulated robot to handle variations in part size and placement.
Learn More About Robotic Drive Technology
Robotic drive systems are a critical component of successful robot implementation, and the field itself offers exciting opportunities for individuals with a passion for industrial technology. If you’re looking to explore educational opportunities in robotics, the Online Robotics website provides helpful resources and insights. Alternatively, you can contact a George Brown College Program Consultant at 1-888-553-5333 to learn more about the Robotics Technician program.