Mastering the Art of Predictive Maintenance: A Game-Changer for Automated Robotics
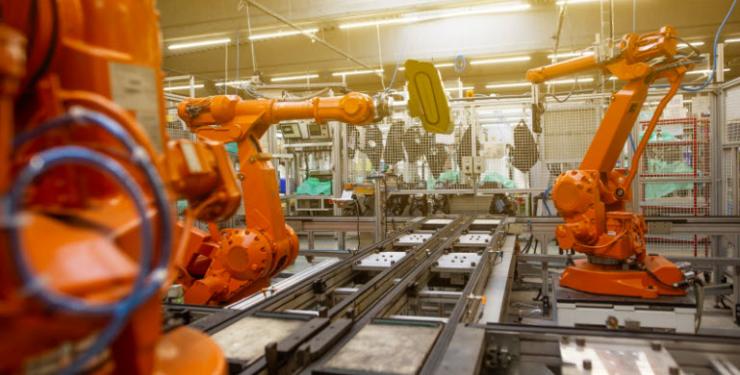
It wasn’t that long ago that performing regular preventative maintenance was the best and only way of ensuring a fleet of expensive industrial robotics remained in good operating condition. Fortunately, this is no longer the case, thanks in part to the integration of AI technologies and data analytics.
As a manufacturer, it is imperative that unscheduled downtime is kept to the absolute minimum. As equipment becomes more complex and operations scale, the predictive maintenance approach to managing assets will not only be the norm of industrial manufacturing, but it will also represent the gold standard.
In this article, we’ll define robotic predictive maintenance and explore the many benefits and advantages therein.
What is Robotic Predictive Maintenance?
As much as the idea has been embedded in lore and pop culture, there is no mystical crystal ball capable of telling us the future. But where mythological clairvoyance has failed, science – particularly artificial intelligence and machine learning – has delivered the next best thing: predictive analytics.
Robotics has certainly revolutionized the industrial and manufacturing sectors, but the technology can be a bit of a double-edged sword; the more automated equipment in use, the more preventative maintenance needs to be scheduled to keep production on point. Traditionally, the strategy has been to perform maintenance on equipment at regular intervals, usually based on the number of operating hours or units produced of a given machine. This approach works reasonably well as it does prolong the life of the equipment, though it does leave significant room for improvement. For example, if an articulated robot receives preventative maintenance every 5,000 hours of operation, how would technicians know of a problem developing at 7,000 hours? If the machine isn’t scheduled to be serviced for another 3,000 operating hours, how likely is it that the problem transforms into a much larger and costlier issue?
Unlike preventative maintenance that relies on a set schedule, predictive maintenance uses data collected from the robotic component itself and leverages advanced algorithms to assess the status of the component in real time. Rather than waiting for the next maintenance date, the articulated robot described above, using predictive maintenance, can predict when a specific maintenance activity should be performed and provide direction on how to resolve the issue.
The Benefits of Predictive Maintenance
The purest benefit of predictive maintenance is targeted maintenance. This means that rather than having a technician circulating the plant performing regular generalized maintenance on a machine that is otherwise functioning optimally, equipment maintenance can be strategically executed to areas/equipment that data has shown to be problematic or that is in imminent danger of failing. Performing inspections that are unnecessary are both costly and time consuming and may not yield any actionable results. By targeting data-backed issues, a facility will not only save time and money on repair activities, but the cost of substantial future repairs will also be minimized.
Benefits - Explored
If being able to switch from a passive to a more targeted maintenance strategy was not enough, predictive maintenance includes these additional benefits:
More Uptime, Increased Productivity
With insights into equipment health provided by source data and analytical tools, maintenance personnel are notified of an issue before the problem has a chance to worsen. This means that rather than having to shut down a machine/production line following a significant failure for a lengthy repair, personnel can preemptively repair or replace the malfunctioning component. While downtime may still be necessary to resolve the issue, there’s a better chance that the repair will take significantly less time, resulting in more uptime and more output.
Equipment Lasts Longer
While both preventative and predictive maintenance share the same goal of ensuring equipment lasts as long as possible, predictive maintenance is arguably much more efficient in realizing this objective. That is because data-driven maintenance effectively reduces the wear and tear on equipment (as failing components can be replaced sooner than they would if a general maintenance schedule was followed) and allows teams to act quickly when a failure is imminent. This expedited maintenance mitigates any tangentially related issues that may arise from not making a repair sooner. In short, the sooner a repair can be made, the greater the likelihood that the equipment will remain operable for longer.
Fewer Maintenance Costs
Considering what we now know of predictive maintenance, it’s easy to see that it can significantly reduce maintenance costs. While predictive maintenance is estimated to save manufacturers roughly 8-12% more than preventative maintenance activities, the disparity is even greater when compared to reactive maintenance (when the equipment operates to failure). Some estimates peg the savings at a whopping 40%. If predictive maintenance is executed quickly, it can reduce reactive maintenance and the associated financial burden to a negligible value.
Predictive Maintenance is Indeed a Game Changer
Once implemented, predictive maintenance processes and methodologies provide an undeniable boost to a manufacturer’s efficiency and cost reduction. Catastrophic failures of equipment and systems will be rare, if not eliminated, and data-driven maintenance activities can be targeted to a specific component or part rather than adhering to a predetermined timeline.
It is inspiring to consider how efficiently even the largest manufacturers can operate when using the power of artificial intelligence, machine learning, and real-world data. If you'd like to be a part of the next wave of robotic technicians that will be an integral part of the predictive maintenance ecosystem, consider enrolling in an online robotics course at George Brown College.