Understanding the Basics of Rotation Position Control
Industrial robotics, as a concept, is one that is understood by a large swath of the population. Rather than relying on dozens or hundreds of human workers to perform repetitive tasks along an assembly line, sophisticated robotics are leveraged to perform the same tasks in less time and with greater accuracy.
What many fail to realize however, is just how much goes into ensuring industrial robotics can properly execute the various actions they are required to perform. This is where rotational position control comes in and what makes industrial robotics possible.
In this article, we’ll examine the challenges in executing position control and provide some real world applications.
What is Rotational Position Control?
The short answer is that rotational position control helps to make robotic automation, as we know it, possible. It is a fundamental pillar of automation, one that involves controlling the position of an axis or servo motor. Control of a rotating body can be achieved using a variety of methods depending on the specific application. Some of the more common methods are described below.
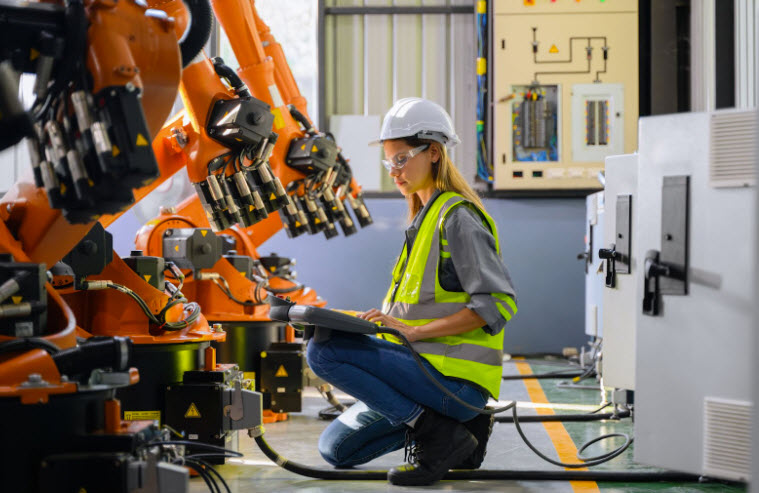
Proportional Integral Derivative (or PID) Control
In layman’s terms, PID control can be summarized thusly. The Proportional term, (P) is used to make immediate positional corrections based on the distance to the target location. The Integral term, (I), is used to make greater positional corrections relative to the speed required to make the correction. Lastly, the Derivative term, (D) makes positional corrections while taking into account how quickly the speed is changing.
Closed-Loop Feedback Systems
In a closed-loop system, devices such as encoders or resolvers are used to provide an accurate position of the rotating body. The system uses that data and compares it to the desired position and makes the necessary adjustments accordingly.
Feedforward Control
Interestingly, a feedforward control system anticipates potential position corrections based on the system’s known dynamics rather than relying on data received by the system. This particular control method facilitates positional corrections that may be required due to external forces that have been applied to the system.
Trajectory Planning
In this control method, algorithms are used to create smooth paths using the initial and ending positions of the rotating body.
It is important to remember that the method used will depend on factors such as accuracy requirements, available resources, etc.
Challenges in Effectuating Position Control
Executing position control is not a cakewalk, by any stretch - even with the sophisticated technologies that make it possible. There are many challenges that make rotation position control possible.
Nonlinear Dynamics
In the real world, varying conditions can impact a system that was designed to rely exclusively using linear controls. These external factors could make accurately controlling the body difficult if not impossible.
Sensor Interference
Interference from other system components like encoders, can generate interference that can impact the efficacy of the positional equipment. As one might expect, accuracy in calibration is vital to rotational position control.
Delay in Execution
Systems that are plagued with high latency or a delay in the control action will experience great difficulty in achieving accurate movements.
External Forces
External forces such as wind, vibrations, and physical impacts can negatively affect a body’s position.
Real Life Applications of Rotational Position Control
The real-world applications that leverage rotational position control are almost too numerous to mention. However, positional control in robotics is necessary anywhere a robotic arm, for example, is used to manipulate components, weld parts, package goods, or access inventory.
Rotation Position Control: A “GPS” for Robotics
Rotation Position Control is a fundamental technology that is crucial for ensuring precision and accuracy when it comes to industrial robotic applications. Understanding how this technology works creates an undeniable appreciation for just how important it is within the manufacturing sector. Whether it’s used to guide an articulated robotic arm or for some other industrial process that requires smooth, precise motion, rotation position control has made possible the continued evolution of automated manufacturing.
As industrial robotic technology progresses, rotation position control will continue to play a critical role in the automated systems, allowing robotics to take on a greater number of tasks with precision and efficiency. If you’re interested in robotics or in a career as a robotics technician, contact George Brown College, toll-free at 1-888-553-5333, and inquire about the Robotics Technician program.